Temperature sensors, often overlooked but vital components, have fundamentally transformed Sensors and Measurement systems in modern technology. These innovative devices act as the sensory organs of numerous systems, enabling them to detect and react to thermal variations in their surroundings. Whether through contact sensors measuring surface temperatures directly or non-contact sensors gauging heat from a distance, temperature sensors are essential for maintaining optimal conditions, ensuring safety, and providing precise control across a wide range of applications. Much like Types of Magnetic Sensors and Type of Optical Sensors, they are critical to modern technological advancements.
The evolution and enhancement of temperature sensors, alongside Types of Magnetic Sensors and Types of Optical Sensors, have been crucial milestones in science and engineering. They have significantly impacted fields from industrial operations to healthcare, facilitating more efficient, safe, and high-performance processes. Whether in home thermostats, spacecraft systems, food processing facilities, or medical devices, temperature sensors in their diverse forms are indispensable for measuring and regulating thermal conditions.
The significance of temperature sensors cannot be overstated. They enable precise thermal process control, improve energy efficiency, enhance operational safety, and increase overall system reliability. Temperature sensors offer several key benefits, including:
- Accurate and real-time temperature measurements across a wide range.
- Automated control of heating and cooling systems in various environments.
- Energy conservation by optimizing thermal processes in industrial and residential settings.
- Enhanced safety by monitoring hazardous conditions in critical applications.
As a result, temperature sensors have become ubiquitous across virtually every industry, from manufacturing and automotive engineering to healthcare and environmental monitoring. They enable advancements in smart home technology, industrial automation, and climate research, continually pushing the boundaries of what is possible in temperature measurement and control, much like Types of Magnetic Sensors and Type of Optical Sensors.
The world of temperature sensors is diverse, encompassing contact and non-contact types, mechanical and electrical varieties, and smart sensors with integrated processing capabilities. This diversity allows for precise temperature measurement across an incredibly wide range of applications and environments, from cryogenic temperatures to extreme heat, and from highly localized measurements to broad area sensing.
As technology advances, the field of temperature sensing evolves, promising even greater accuracy, efficiency, and integration in the future. Understanding the various types and applications of temperature sensors, alongside other crucial categories like Types of Magnetic Sensors and Type of Optical Sensors, is essential for anyone involved in fields where thermal management plays a key role, paving the way for innovative solutions to complex temperature-related challenges.
The types of electrical temperature sensors, while distinct in their output, share fundamental principles with other sensor categories. Like mechanical sensors, many electrical sensors rely on temperature-induced physical changes in materials. Instead of producing mechanical motion, they generate electrical signals. Some, such as thermopiles, even share similarities with non-contact sensors by measuring temperature without direct contact. This overlap across sensor types highlights the diverse ways in which temperature can be measured, with each method optimized for specific applications. Understanding these similarities and differences is crucial for selecting the most appropriate sensor, considering factors such as accuracy, temperature range, response time, and environmental conditions.
Different Types of Temperature Sensors
The world of temperature sensors is diverse, with various types designed to measure specific temperature ranges, operate in particular environments, or suit specific applications. Understanding these different types is crucial for engineers, technicians, and anyone involved in temperature measurement and control. Here are the main categories of temperature sensors:
- Contact Temperature Sensors
- Non-Contact Temperature Sensors
- Mechanical Temperature Sensors
- Electrical Temperature Sensors
- Smart/Digital Temperature Sensors
Each of these temperature sensor categories encompasses various specific sensor types, each with its own set of characteristics, advantages, and limitations, making them suitable for different applications across various industries. The choice of temperature sensor depends on factors such as temperature range, accuracy requirements, response time, environmental conditions, and cost considerations. The selection of the appropriate temperature sensor category and specific type is crucial in ensuring accurate measurements, efficient processes, and safe operations. As technology advances, new types of temperature sensors continue to emerge within these categories, expanding the possibilities for more precise and versatile temperature sensing across an ever-growing range of applications.
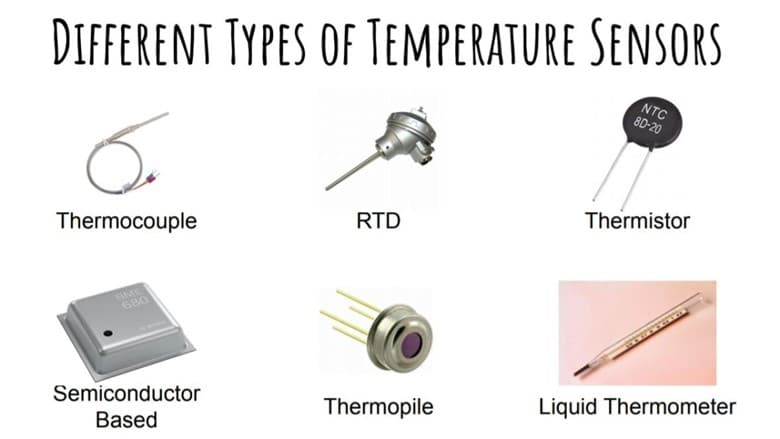
Types of Temperature Sensors in Table
Sensor Type | Key Features | Common Applications | Advantages | Disadvantages | Cost |
Contact Temperature Sensors | – Direct physical contact with object – Various subtypes (thermocouples, RTDs, thermistors) |
– Industrial processes – HVAC systems – Automotive industry – Food and beverage production |
– High accuracy – Wide temperature range – Robust for harsh environments |
– Require physical contact – May alter object temperature – Slower response times |
Relatively low cost, especially for basic types |
Non-Contact Temperature Sensors | – Measure temperature without physical contact – Use infrared radiation detection |
– Industrial processes – HVAC systems – Food processing – Medical diagnostics |
– Can measure moving objects – Fast response times – No wear and tear |
– Affected by emissivity – Measure only surface temperature – Line of sight required |
Can be more expensive than contact sensors |
Mechanical Temperature Sensors | – Use thermal expansion of materials – Convert temperature to mechanical motion |
– HVAC systems – Home appliances – Medical field – Environmental monitoring |
– Simple design – No electrical power required – Direct visual readings |
– Limited temperature range – Slower response times – Difficult to integrate with electronic systems |
Generally low cost |
Electrical Temperature Sensors | – Convert thermal energy to electrical signals – Include thermocouples, RTDs, thermistors |
– Automation and process control – Industrial machinery – Automotive and aerospace – Consumer electronics |
– High accuracy – Easy integration with electronic systems – Wide temperature range |
– Require power source – May be sensitive to EMI – Some types need calibration |
Can be more expensive than mechanical sensors |
Smart/Digital Temperature Sensors | – Combine sensing with digital processing – Often include wireless connectivity |
– Smart home systems – IoT applications – Advanced industrial control – Healthcare monitoring |
– Wireless connectivity – Integration with smart systems – Real-time alerts and data logging |
– Higher cost – Potential privacy concerns – Dependent on wireless networks |
Generally the most expensive option |
What are Contact Temperature Sensors?
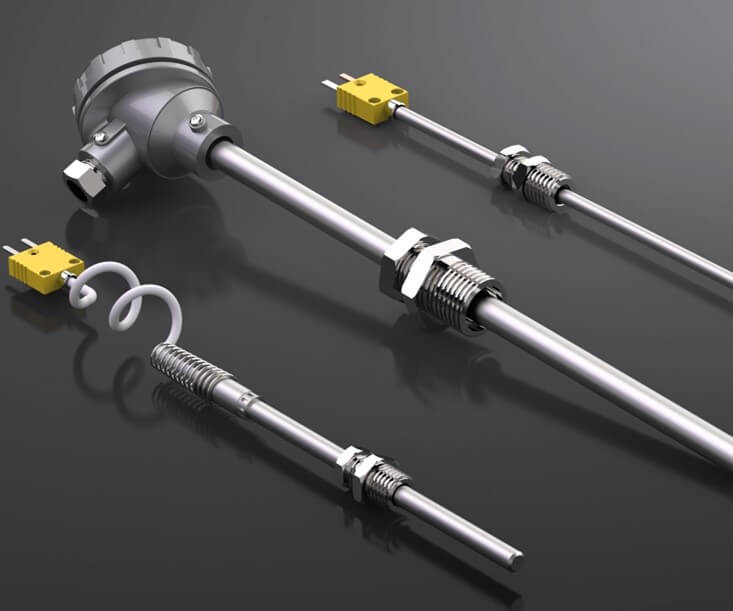
Contact temperature sensors are devices that measure temperature by directly touching or being in physical contact with the object or substance being measured. These sensors are widely used in various industrial, commercial, and residential applications where accurate temperature readings are critical for controlling and maintaining desired thermal conditions.
Working Principle of Contact Temperature Sensors
Contact temperature sensors operate on the principle of heat transfer from the object to the sensor. They measure the temperature by detecting changes in physical properties of their sensing elements when exposed to different temperatures. The specific working principle varies depending on the type of contact sensor:
- Thermocouples generate a voltage based on the temperature difference between two dissimilar metal wires.
- Thermistors measure changes in electrical resistance of a semiconductor material as temperature varies.
- Resistance Temperature Detectors (RTDs) detect temperature-induced changes in the resistance of a metal wire, typically platinum.
Applications of Contact Temperature Sensors
Contact temperature sensors find applications in numerous fields, including:
- Industrial processes and manufacturing
- HVAC systems in buildings
- Automotive industry for engine temperature monitoring
- Food and beverage production
- Medical equipment and diagnostics
- Scientific research and laboratories
- Consumer electronics
Types of Contact Temperature Sensors
Contact temperature sensors come in several types, each with its own unique characteristics and applications:
- Thermocouples: These sensors are composed of two dissimilar metal wires joined at one end. They generate a small voltage proportional to the temperature difference between the junction and reference point. Thermocouples are known for their wide temperature range, ruggedness, and low cost. They are commonly used in industrial processes, kilns, and engine systems.
- Resistance Temperature Detectors (RTDs): RTDs use a pure metal, usually platinum, as their sensing element. The electrical resistance of the metal increases with temperature in a predictable manner. RTDs offer high accuracy and excellent stability, making them ideal for precision applications in food processing, pharmaceutical manufacturing, and laboratories.
- Thermistors: Made from ceramic semiconductor material, thermistors exhibit significant resistance changes with temperature. They can have either a negative or positive temperature coefficient. Thermistors are highly sensitive and respond quickly to temperature changes, making them suitable for applications requiring precise measurements over a narrow range, such as in medical devices and HVAC systems.
- Semiconductor Sensors: These sensors utilize the temperature-dependent characteristics of semiconductor p-n junctions. They provide a linear output and are easily integrated with electronic circuits. Semiconductor sensors are commonly found in consumer electronics, computer hardware, and automotive systems.
- Liquid-in-Glass Thermometers: While less common in modern industrial applications, liquid-in-glass thermometers still find use in basic temperature monitoring. They consist of a glass tube filled with a liquid (typically alcohol, as mercury is being phased out) that expands or contracts with temperature changes, moving along a calibrated scale.
- Bimetallic Strip Thermometers: These simple devices are made of two strips of different metals bonded together. The different thermal expansion rates of the metals cause the strip to bend with temperature changes. Bimetallic strip thermometers are often used in thermostats and basic temperature control systems.
Each type of contact temperature sensor has its strengths and is chosen based on the specific requirements of the application, such as temperature range, accuracy needs, response time, and cost considerations.
Advantages of Contact Temperature Sensors
- High accuracy and precision in temperature measurement
- Wide temperature range capability
- Relatively low cost, especially for basic types
- Robust and suitable for harsh industrial environments
- Direct measurement without interference from surrounding radiation
Disadvantages of Contact Temperature Sensors
- Require physical contact, which may not be feasible or safe in some situations
- Can potentially alter the temperature of the object being measured
- May have slower response times compared to non-contact sensors
- Subject to wear and tear due to physical contact
- Limited use in moving or rotating equipment
- Some types may require periodic calibration to maintain accuracy
Contact temperature sensors remain a fundamental tool in temperature measurement across various industries. Their ability to provide accurate, direct temperature readings makes them indispensable in many applications, despite some limitations. The choice of specific sensor type depends on the particular requirements of each application, including temperature range, accuracy needs, and environmental conditions.
What are non-Contact Temperature Sensors?
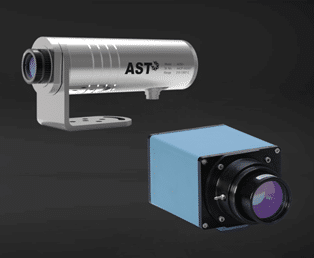
Non-contact temperature sensors are devices that measure the temperature of an object without physically touching it. These sensors detect the infrared radiation emitted by the object to determine its temperature. They are often referred to as infrared sensors and are used in various industrial and scientific applications where direct contact with the object is not possible or desirable.
Working Principle of non-Contact Temperature Sensors
Non-contact temperature sensors operate on the principle of detecting infrared radiation. All objects above absolute zero temperature emit infrared radiation. The sensor measures the intensity of this radiation, which is proportional to the object’s temperature. The sensor then converts this measurement into a temperature reading. The accuracy of the measurement depends on factors such as the object’s emissivity, the distance to the object, and environmental conditions.
Applications of non-Contact Temperature Sensors
Non-contact temperature sensors find applications in numerous fields, including:
- Industrial processes for monitoring equipment and product temperatures
- HVAC systems for building climate control
- Food processing and storage temperature monitoring
- Medical and veterinary diagnostics
- Automotive industry for engine and tire temperature monitoring
- Firefighting and building inspections
- Research and development in various scientific fields
Types of non-Contact Temperature Sensors
- Infrared Thermometers: These handheld devices measure temperature by detecting the infrared radiation emitted from an object’s surface. They are widely used for quick and easy temperature measurements in various applications.
- Pyrometers: These are more sophisticated infrared sensors designed for high-temperature measurements. They are often used in industrial settings for monitoring processes involving metals, glass, or ceramics.
- Thermal Imaging Cameras: These devices create a visual representation of the temperature distribution across an entire area. They are used for detecting hot spots, heat loss, and temperature patterns in large areas or complex systems.
- Fiber Optic Sensors: These sensors use optical fibers to transmit infrared radiation from the target to a remote detector. They are particularly useful in environments with high electromagnetic interference or where space is limited.
Advantages of non-Contact Temperature Sensors
Non-contact temperature sensors offer several benefits:
- They can measure temperatures of moving or hard-to-reach objects
- They allow for measurements of very high temperatures without sensor damage
- They provide fast response times and can quickly detect temperature changes
- They don’t interfere with the temperature of the object being measured
- They can be used in hazardous or sterile environments where contact is not possible or desirable
- They have no wear and tear due to lack of physical contact
Disadvantages of non-Contact Temperature Sensors
Despite their advantages, non-contact sensors have some limitations:
- They typically measure only surface temperatures
- Their accuracy can be affected by the object’s emissivity and environmental factors
- They may have difficulty measuring through gases or vacuum
- They can be more expensive than contact sensors
- They may require a clear line of sight to the object being measured
- Their accuracy may be lower than contact sensors in some applications
What are Mechanical Temperature Sensors?
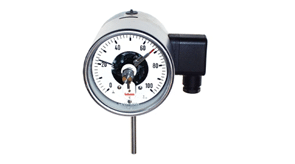
Mechanical temperature sensors are devices that measure temperature by utilizing the physical changes that occur in materials due to temperature variations. These sensors convert temperature changes into mechanical motion, which can be observed or measured directly. They are among the oldest and most widely used temperature measuring devices, often providing reliable measurements without the need for electrical power.
Working Principle of Mechanical Temperature Sensors
Mechanical temperature sensors operate on the principle of thermal expansion or contraction of materials. As temperature changes, most materials expand when heated and contract when cooled. This change in physical dimensions is used to indicate temperature. The degree of expansion or contraction is calibrated to correspond to specific temperature readings.
Applications of Mechanical Temperature Sensors
Mechanical temperature sensors find applications in various fields, including:
- Industrial processes for monitoring equipment temperatures
- HVAC systems for building climate control
- Medical field for body temperature measurements
- Food preparation and storage
- Automotive industry for engine temperature monitoring
- Home appliances like ovens and refrigerators
- Environmental monitoring in greenhouses or aquariums
Types of Mechanical Temperature Sensors
- Liquid-in-Glass Thermometers: These common devices use the expansion of a liquid (usually mercury or alcohol) in a glass tube to indicate temperature. They are widely used for measuring body temperature and ambient temperatures.
- Bimetallic Strip Thermometers: These sensors consist of two different metals bonded together. As temperature changes, the metals expand at different rates, causing the strip to bend. This bending is used to move a pointer across a temperature scale or to actuate switches in thermostats.
- Bulb and Capillary Sensors: These use the expansion of a fluid (liquid, gas, or vapor) in a sealed system to measure temperature. They are often used in industrial and HVAC applications.
- Gas Pressure Thermometers: These devices use the change in pressure of a gas in a sealed system to indicate temperature changes. They are useful for measuring temperatures in remote locations.
Advantages of Mechanical Temperature Sensors
Mechanical temperature sensors offer several benefits:
- Simple design and easy to use
- Do not require electrical power to operate
- Generally low cost and widely available
- Durable and suitable for harsh environments
- Provide direct, visual temperature readings
- Can be highly accurate within their designed range
Disadvantages of Mechanical Temperature Sensors
Despite their advantages, mechanical sensors have some limitations:
- Limited temperature range compared to some electronic sensors
- Cannot be easily integrated into electronic systems for data logging or control
- May have slower response times than electronic sensors
- Some types (like mercury thermometers) pose environmental or safety risks
- Limited ability for remote monitoring
- May require manual reading and recording of measurements
What are Electrical Temperature Sensors?
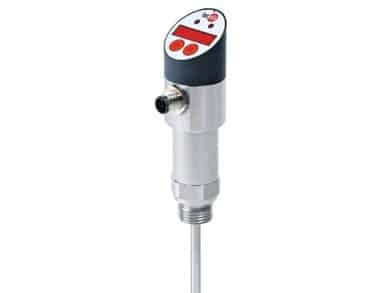
Electrical temperature sensors are electronic devices that measure temperature by converting thermal energy into electrical signals. These sensors utilize temperature-dependent electrical properties of materials to provide accurate and easily transmittable temperature readings. They have become indispensable in modern automation, consumer goods, and industrial applications due to their versatility and precision.
Working Principle of Electrical Temperature Sensors
Electrical temperature sensors operate on the principle of temperature-dependent changes in electrical properties. As temperature changes, these sensors exhibit variations in resistance, voltage, or current. These changes are then converted into standardized electrical signals that can be easily measured, processed, and integrated into control systems.
Applications of Electrical Temperature Sensors
Electrical temperature sensors find applications in numerous fields, including:
- Automation and process control
- Heating, ventilation, and air conditioning (HVAC) systems
- Refrigeration and cold storage
- Environmental monitoring
- Water and wastewater treatment
- Industrial machinery and motor monitoring
- Power generation and distribution
- Chemical and process engineering
- Automotive and aerospace industries
- Consumer electronics and appliances
Types of Electrical Temperature Sensors
- Thermocouples: These sensors consist of two dissimilar metal wires joined at one end. They generate a small voltage proportional to the temperature difference between the junction and the reference point. Thermocouples are known for their wide temperature range and ruggedness.
- Resistance Temperature Detectors (RTDs): RTDs use the principle of temperature-dependent resistance in pure metals, typically platinum. They offer high accuracy and stability over a wide temperature range, making them ideal for precision applications.
- Thermistors: These sensors are made from semiconductor materials whose resistance changes significantly with temperature. Thermistors can be either Negative Temperature Coefficient (NTC) or Positive Temperature Coefficient (PTC) types. They offer high sensitivity and are commonly used in applications requiring precise temperature control.
Advantages of Electrical Temperature Sensors
Electrical temperature sensors offer several benefits:
- High accuracy and precision in temperature measurement
- Easy integration with electronic control and monitoring systems
- Capability for remote sensing and data logging
- Wide temperature range coverage
- Fast response times
- Suitability for automation and process control
- Durability and long-term stability
- Availability in various forms for different applications
Disadvantages of Electrical Temperature Sensors
Despite their advantages, electrical sensors have some limitations:
- Require a power source to operate
- May be sensitive to electromagnetic interference
- Some types (like thermocouples) require cold junction compensation
- Can be more expensive than simple mechanical sensors
- May require periodic calibration to maintain accuracy
- Some types have limited temperature ranges compared to others
What are Smart/Digital Temperature Sensors?
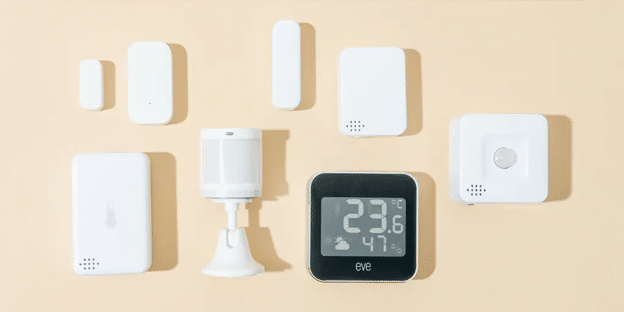
Smart or digital temperature sensors are advanced electronic devices designed to measure temperature by converting thermal energy into digital signals. These sensors utilize temperature-dependent electrical properties of materials to provide accurate and easily transmittable temperature readings. They integrate additional features such as wireless connectivity, data processing capabilities, and compatibility with smart home systems. These sensors have become essential in modern automation, consumer goods, and industrial applications due to their versatility, precision, and enhanced functionality.
Working Principle of Smart/Digital Temperature Sensors
Smart/digital temperature sensors operate on the principle of temperature-dependent changes in electrical properties. As temperature changes, these sensors exhibit variations in resistance, voltage, or current. These changes are converted into standardized electrical signals that are digitized for easy measurement, processing, and integration into control systems. These digital signals can be transmitted wirelessly via Bluetooth or Wi-Fi to a central hub or smartphone app for real-time monitoring and control.
Applications of Smart/Digital Temperature Sensors
Smart/digital temperature sensors find applications in numerous fields, including:
- Automation and process control
- Heating, ventilation, and air conditioning (HVAC) systems
- Refrigeration and cold storage
- Environmental monitoring
- Water and wastewater treatment
- Industrial machinery and motor monitoring
- Power generation and distribution
- Chemical and process engineering
- Automotive and aerospace industries
- Consumer electronics and appliances
- Smart home systems and energy management
- Healthcare for body temperature monitoring
- Food and beverage industry for safety and quality control
Types of Smart/Digital Temperature Sensors
- Thermocouples: These sensors consist of two dissimilar metal wires joined at one end. They generate a small voltage proportional to the temperature difference between the junction and the reference point. Thermocouples are known for their wide temperature range and ruggedness.
- Resistance Temperature Detectors (RTDs): RTDs use the principle of temperature-dependent resistance in pure metals, typically platinum. They offer high accuracy and stability over a wide temperature range, making them ideal for precision applications.
- Thermistors: These sensors are made from semiconductor materials whose resistance changes significantly with temperature. Thermistors can be either Negative Temperature Coefficient (NTC) or Positive Temperature Coefficient (PTC) types. They offer high sensitivity and are commonly used in applications requiring precise temperature control.
- Digital Temperature Sensors: These are integrated circuits that combine sensing elements with signal processing capabilities. They often provide a digital output, making them easy to interface with microcontrollers and other digital systems.
- Smart Temperature Sensors: These advanced sensors combine temperature sensing with wireless connectivity (Bluetooth or Wi-Fi) and often include additional features like humidity sensing. They can communicate with smart thermostats and mobile apps for remote monitoring and control.
Advantages of Smart/Digital Temperature Sensors
Smart/digital temperature sensors offer several benefits:
- High accuracy and precision in temperature measurement
- Easy integration with electronic control and monitoring systems
- Capability for remote sensing and data logging
- Wide temperature range coverage
- Fast response times
- Suitability for automation and process control
- Durability and long-term stability
- Availability in various forms for different applications
- Wireless connectivity and smartphone integration
- Energy efficiency through intelligent temperature management
- Multi-zone temperature control in smart home applications
- Real-time alerts and notifications for temperature changes
Disadvantages of Smart/Digital Temperature Sensors
Despite their advantages, smart/digital sensors have some limitations:
- Require a power source to operate
- May be sensitive to electromagnetic interference
- Some types (like thermocouples) require cold junction compensation
- Can be more expensive than simple mechanical sensors
- May require periodic calibration to maintain accuracy
- Some types have limited temperature ranges compared to others
- Smart sensors may have privacy concerns due to data collection
- Potential for cybersecurity risks in connected smart sensor systems
- Dependency on wireless networks for smart sensor functionality
Smart and digital temperature sensors represent a significant advancement in temperature measurement technology. They combine the precision of traditional temperature sensing with the convenience of digital processing and wireless connectivity, making them invaluable in a wide range of applications from industrial processes to smart home systems. While they present some challenges, their benefits in terms of accuracy, ease of use, and integration capabilities make them an increasingly popular choice in many fields.
Conclusion
Temperature sensors are integral components in a wide array of applications, from industrial processes to smart home systems. The diverse types of sensors – contact, non-contact, mechanical, electrical, and smart/digital – each offer unique advantages and are suited to specific use cases. As technology continues to advance, we’re seeing a shift towards more sophisticated sensors, particularly in the realm of smart and digital temperature sensors. These modern sensors not only provide accurate temperature readings but also offer enhanced features like wireless connectivity, data processing, and integration with other smart systems.
While each type of sensor has its strengths and limitations, the choice of sensor ultimately depends on the specific requirements of the application, including factors such as temperature range, accuracy needs, environmental conditions, and cost considerations. As we move forward, the development of temperature sensing technology is likely to focus on improving accuracy, expanding connectivity options, and enhancing energy efficiency. This ongoing evolution in temperature sensing technology will continue to play a crucial role in advancing various fields, from healthcare and environmental monitoring to industrial automation and smart home systems.
FAQs about Types of Temperature Sensors:
- What is the main difference between contact and non-contact temperature sensors?
Contact temperature sensors require physical contact with the object being measured, while non-contact sensors can measure temperature from a distance by detecting infrared radiation emitted by the object. - Which type of temperature sensor is most accurate?
Generally, Resistance Temperature Detectors (RTDs) are considered to be among the most accurate temperature sensors. However, the accuracy can depend on the specific application and environmental conditions. - What are the advantages of using smart temperature sensors?
Smart temperature sensors offer benefits such as wireless connectivity, integration with smart home systems, remote monitoring and control, real-time alerts, and often additional features like humidity sensing. - Can temperature sensors work in extreme environments?
Yes, certain types of temperature sensors are designed to work in extreme environments. For example, thermocouples can measure very high temperatures in industrial settings, while specially designed sensors can operate in cryogenic conditions. - How often do temperature sensors need to be calibrated?
The calibration frequency depends on the type of sensor, its application, and the required accuracy. Some sensors may need calibration annually, while others can go several years between calibrations. It’s best to follow manufacturer recommendations and industry standards for your specific application. - What is the difference between a thermistor and an RTD?
Thermistors are made from semiconductor materials and offer high sensitivity over a relatively narrow temperature range. RTDs use pure metals (often platinum) and provide high accuracy over a wider temperature range. Thermistors are generally less expensive but less stable over time compared to RTDs.